If you are a pedal brand looking for a pedal manufacturer you’ll discover
- what you should expect from a quality manufacturer, and
- what questions to ask to better pre-qualify a firm for your short list.
If you’re just looking for insight into bike manufacturing in general, you’ll also find rarely-shared details of manufacturing processes many companies keep out of sight.
CONTENTS
‘Upstream’ and ‘Downstream’ in the Bike Manufacturing Supply Chain
3 Types of Manufacturers
4 Stages in Pedal Manufacturing
1. Design Stage
2. CNC Stage
3. Assembly Stage
4. Testing Stage
UPSTREAM AND DOWNSTREAM IN THE MANUFACTURING SUPPLY CHAIN
Manufacturers lie on a scale according to how much processing is done within their own factory versus processing tasks they contract to have done by other, usually smaller and more specialized, workshops.
These workshops are said to be situated ‘upstream’ or ‘downstream’ relative to each other.
The further upstream a workshop is located, the more specialized the processing.
The bicycle supply chain is a long and winding road — or river, to be consistent — that can be roughly divided into three types.
- Firms that operate close to the source and do most, if not all, of their own processing in-house.
- A lot of in-house processing as well as outsourced; low level through to full assembly for less complex products
- Little in-house processing or very specialized, mainly assembling complex products such as complete bikes
Many companies straddle these categories of course, fitting more into one than another.
1. Close-to-the-Source, ‘Tributary’ Producers
Some factories in the supply chain for the bicycle industry commence manufacturing close to the raw ingredients.
The main metals are bauxite (the base ore from which aluminum is extracted), iron ore for stainless steel, and rutile or ilmenite for titanium.
Chemical companies blend BPA and ECH to create the epoxy resin that binds carbon fibers; manufacturing carbon fibers involves the carbonization of polyacrylonitrile, and to a lesser extent rayon or petroleum pitch, removing non-carbon atoms.
This ‘precursor’ material is then pulled into fibers and treated to improve their bondability with epoxy resins, then further woven into the signature cloth form of carbon composites.
Carbon composite manufacturers are closest to the source since they take carbon fiber from the manufacturer — one step removed from the Chemical company source — for insertion into molds to create components.
2. Elementary Manufacturers or Service Providers
Elementary doesn’t mean simple.
Base materials enter the first level of the bicycle supply chain anywhere from a small nuts-and-bolts workshop to a medium sized multi-process factory.
Heat treatment of aluminum alloy components, for example, is offered by factories who do nothing else, and provide heat treatment services for a variety of components.
The further downstream a factory is located, the greater the range of generic processing which ends up in final product assembly.
A company like Kaoshiung’s Kinlin Industrial Corp., maker of bike wheel rims, works directly with aluminum billets imported directly from the smelter (eg. Portland, Australia), which they heat and press into rims.
Specialist wheel brands, or bike brands who build their own wheel sets, purchase Kinlin’s rims for assembly into wheels.
Or, having also purchased spokes and hubs from local suppliers, send the lot to a specialist manufacturer such as Saint Jump Wheelcrafters in Taichung’s Houli district.
3. Comprehensive – More Assembly than Manufacturing
Companies in this category are located a long way downstream.
They purchase a wide variety of components and assemble them into complete bikes or the complete product of whatever it is they make.
They may do some key processing, particularly CNC, and perhaps frame manufacturing.
Assembly is handled in-house. Completed products are boxed up for shipping to customers.
Complete bikes are usually partially assembled with bike shop mechanics completing builds for customers to ride away on.
SCADA ships pedals fully assembled, the overall operation being a combination of #1 and #2.
4 STAGES IN (PEDAL) MANUFACTURING
Although the following sections concentrate on pedal manufacturing processes, the same techniques are used in manufacturing other bike components.
The planning and design stage sets up a manufacturing project by producing CAD blueprints, then deciding on which other components will be used.
The CNC manufacturing stage takes those blueprints, converted into CNC G-code, and executes component processing.
I focus on CNC here because it’s mostly what we do. Die casting is also used in the pedal manufacturing process, and we do produce a number of models for a range of clients using this method..
In the assembly stage we take the components we process ourselves together with components sourced downstream to create complete pedal sets, boxed up pairs of pedals ready for the consumer, or for installation by assembly companies on complete bikes, including exercise bikes (we supply some of the the biggest exercise bike names).
The final stage is testing where we select units from a batch or take a new design prototype and test them against a standard before mass production of a batch incorporating the component can go ahead.
DESIGN STAGE
Bike components often begin life as rough drawing on a sketch pad or even a scrap piece of paper (the classic sketch on the back of a napkin to capture an idea while it’s fresh actually exists…).
Video begins at the ‘design’ stage section.
Once those few rough sketches are formalized inside CAD, the magic can begin.
More than simply a design blueprint for the component, the final model will form the basis for the program to be executed by the CNC machine which will cut the main form as well as etch out smaller details such as the grip pin holes.
I’ll illustrate how this process unfolds using the example of the development of a new mountain bike flat pedal (or road bike, depending on the specific use case).
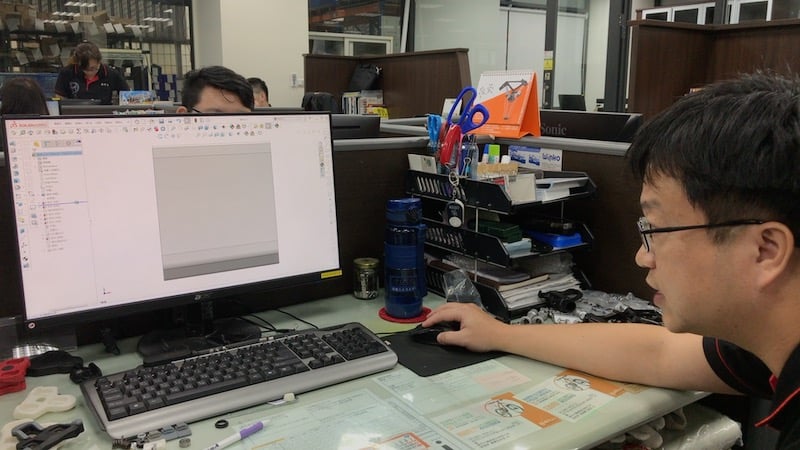
We start with a blank pedal body scaled to the length and breadth of the finished pedal in CAD.
The physical aluminum blank actually enters the manufacturing process as represented in the CAD diagram (I’ll cover the machining of such a blank below).
The CNC program follows the instructions mapped out in CAD to cut the alloy, as per the design, down to the last detail.
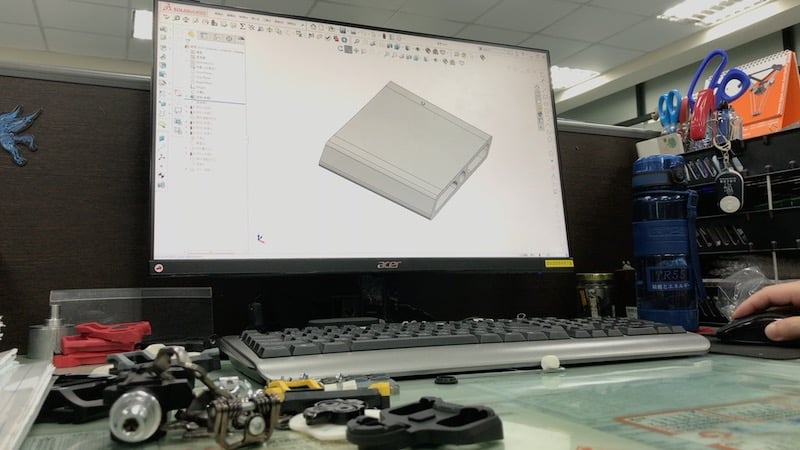
Rotating the image reveals the hollowed interior forming the two levels of the platform in this pedal design.
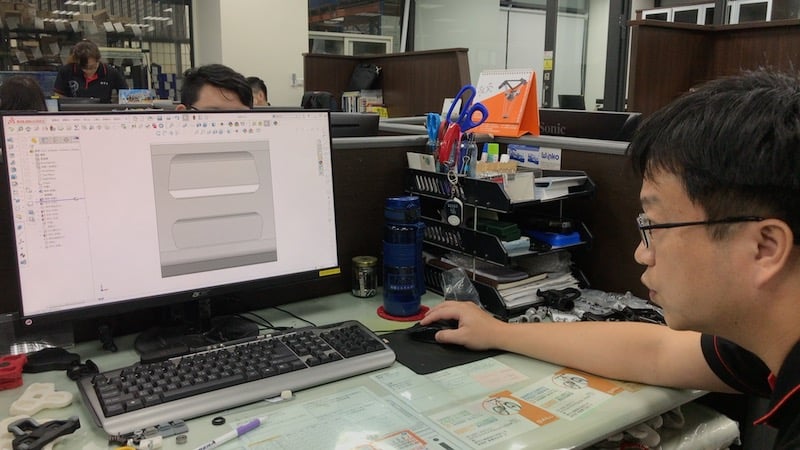
The designer begins to map out the sections of the platform to be removed during CNC machining.
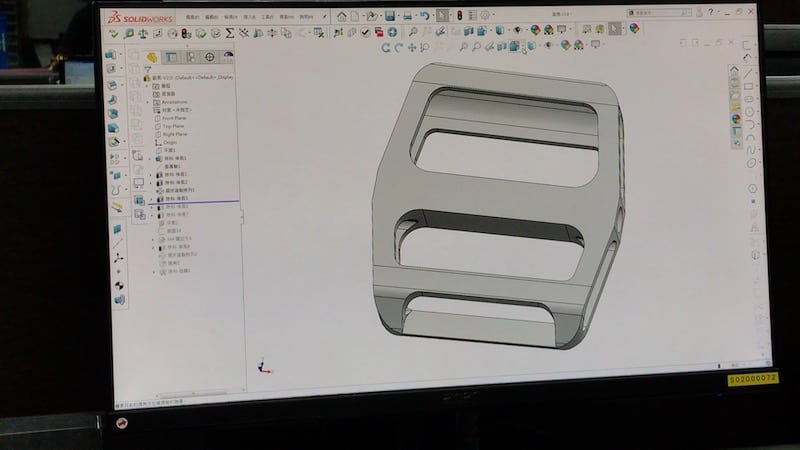
That’s the crude form of the pedal body ready to add the spec that will make this design unique — and complete.
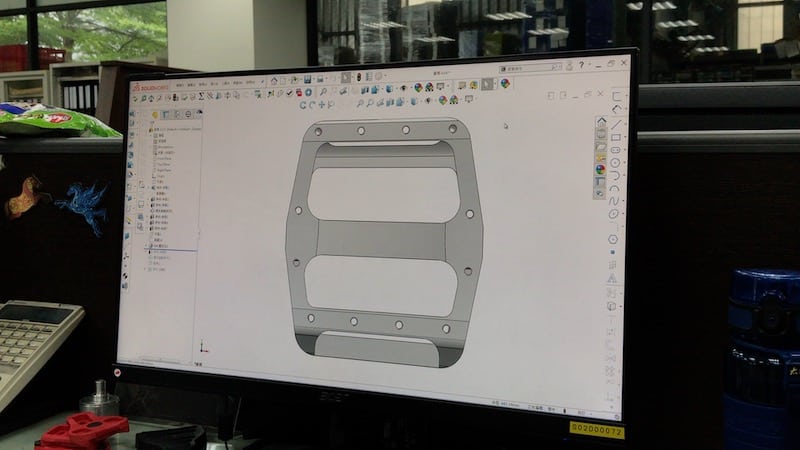
The design calls for 12 pins per pedal evenly distributed, with four at the front, four at the back, and two on either side in the middle.

Next step is to add the countersink profile since the pins will be hex-head removable and adjustable.
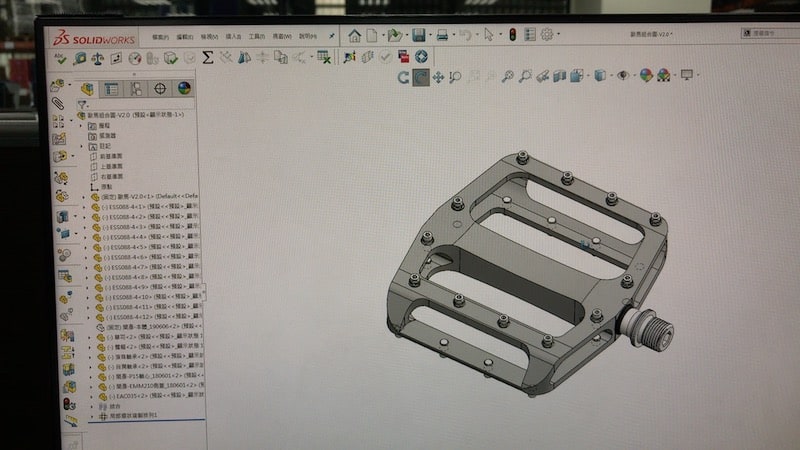
Adding the pins and axle gives a complete structural view of the pedal which excludes the finishing details.
The pedal body will be finished by anodizing, and the branding laser-etched into it before the pins and axle are installed. This happens at the very end, as we’ll see in the section on assembly.
A key aspect determining the final design is cost, of course. Using nylon, for example, to produce basic but nonetheless sophisticated designs allows for pedals targeting those cyclists happy with that level of product.
CNC-machined alloy makes complex designs of greater durability possible, of course.
CNC STAGE
Take a look into any bicycle factory in Taiwan and you’ll see at least one CNC machine in 999 out of 1000 establishments.
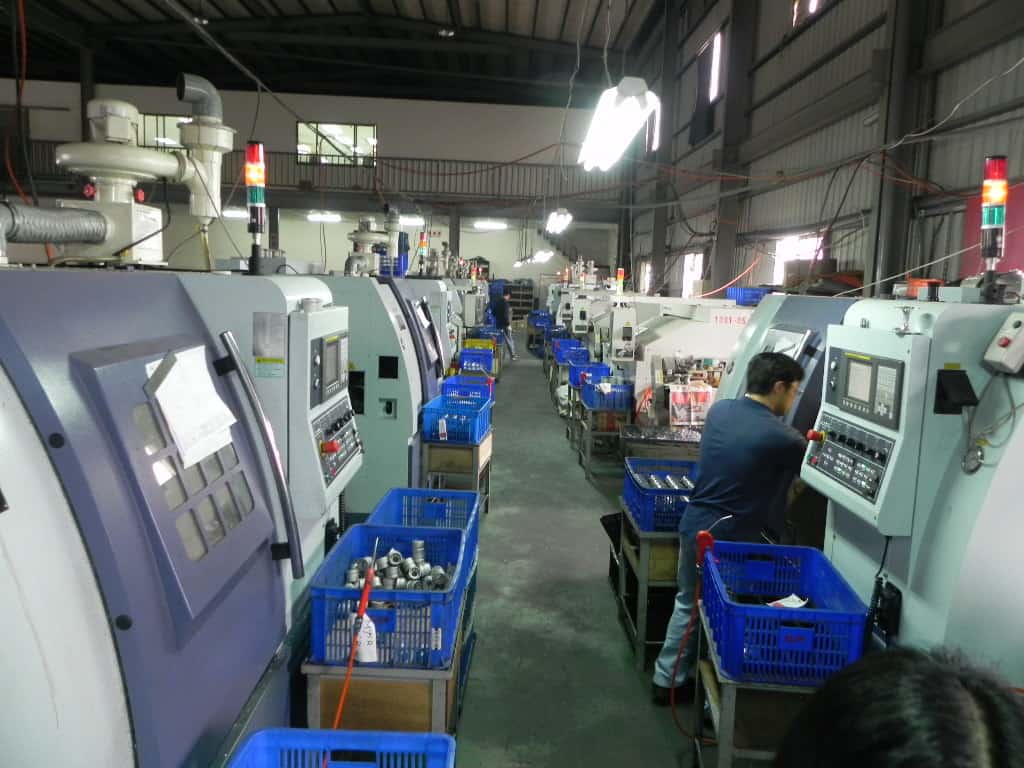
Many factories are set up like this one and contain dozens of machines.
The beauty of CNC machining is the customization it makes possible—almost any imagined design can be realized.
Bike pedals are routinely manufactured from die-cast aluminum or from molded nylon.
However, a block of aluminum can be carved into any shape able to be drawn up in CAD (where the sky is almost the limit) to exacting tolerances.
Operating the Machines
CNC machines are not particularly complicated but still require expertise — and experience — to operate properly.
Operators know their machines well and since machining jobs are processed in batches, anomalies are quickly discovered.
Operators and QC supervisors routinely inspect and measure sample items out of a batch to ensure machining is within the prescribed tolerances.
CNC machining usually proceeds one piece at a time for specialized components or serially across several components fitted on a platform or revolving drum.
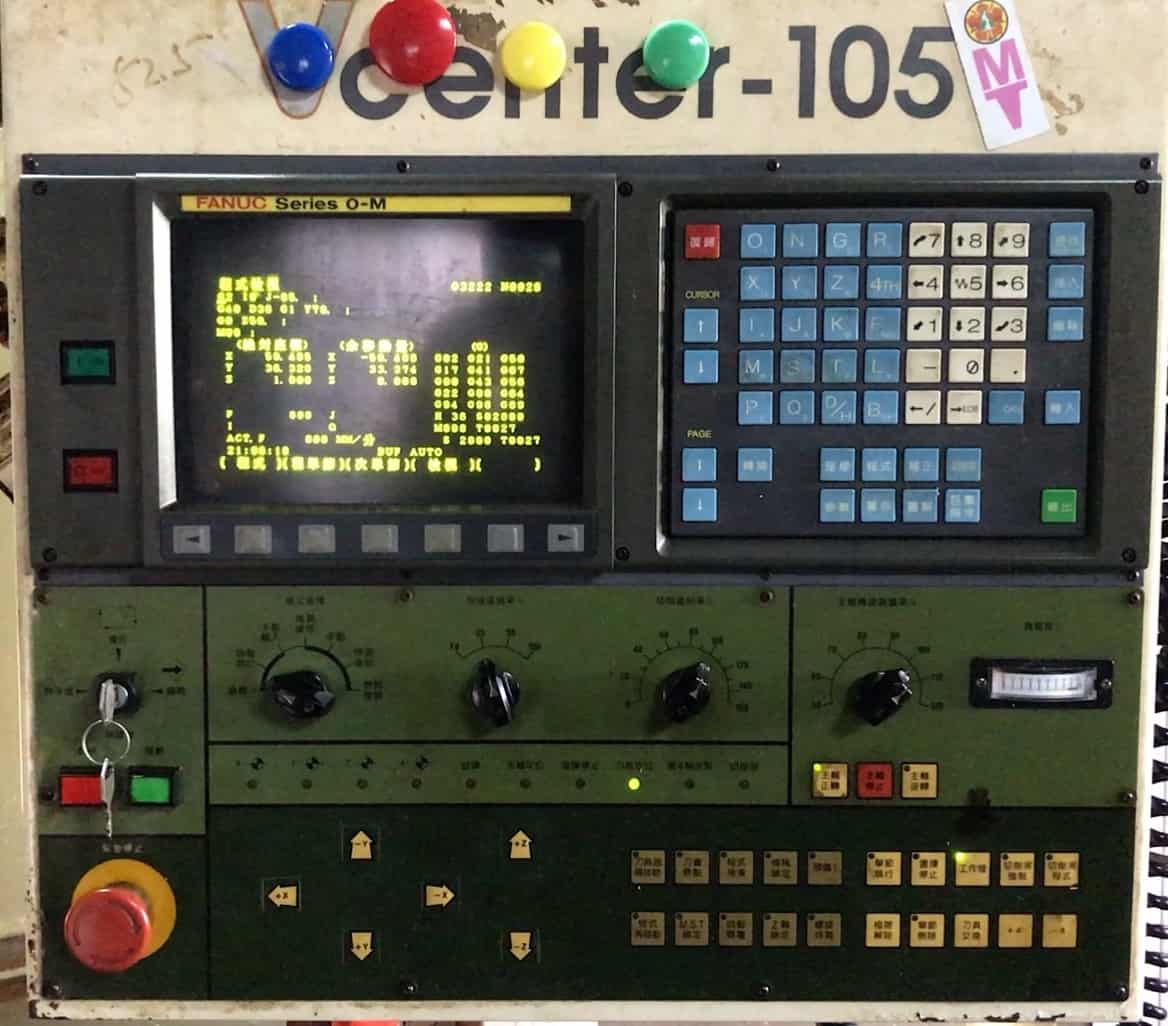
The progress of one processing cycle plays out on the monitor as the program executes.
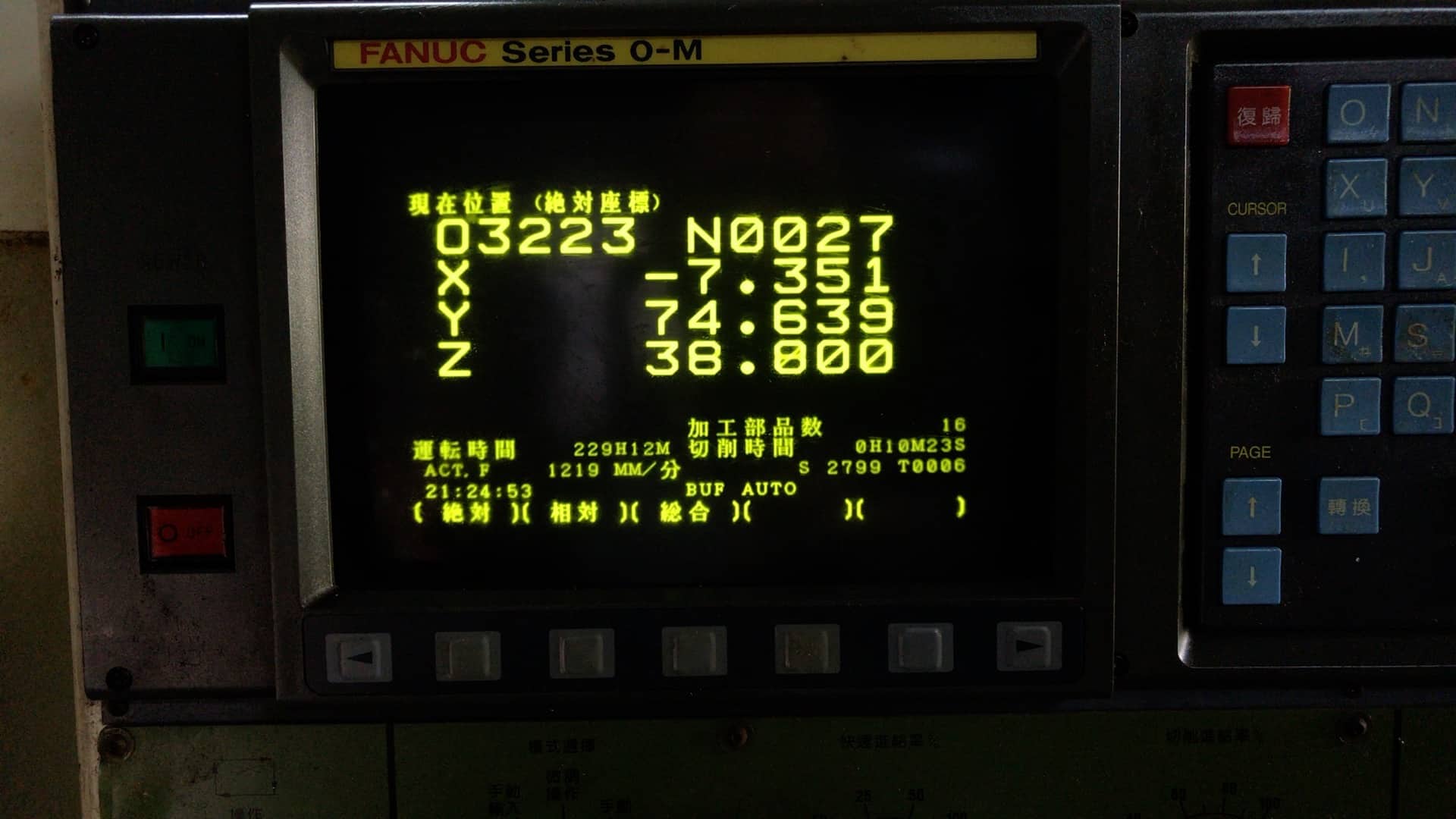
Three dimensions are represented by the X, Y and Z axes.
Cutter heads move left and right along the X axis, forward and back along the Y axis, up and down along the Z axis.
X, Y, and Z in combination with the ability to rotate through 180 degrees enabling finely chamfered flat, concave, or convex edges makes any practical design possible.
One cycle is one complete cutting sequence whether performed on one piece or several simultaneously.
Once a cycle is complete, the operator removes the piece or pieces, replaces them with uncut components, then hits the start button to commence the cut.
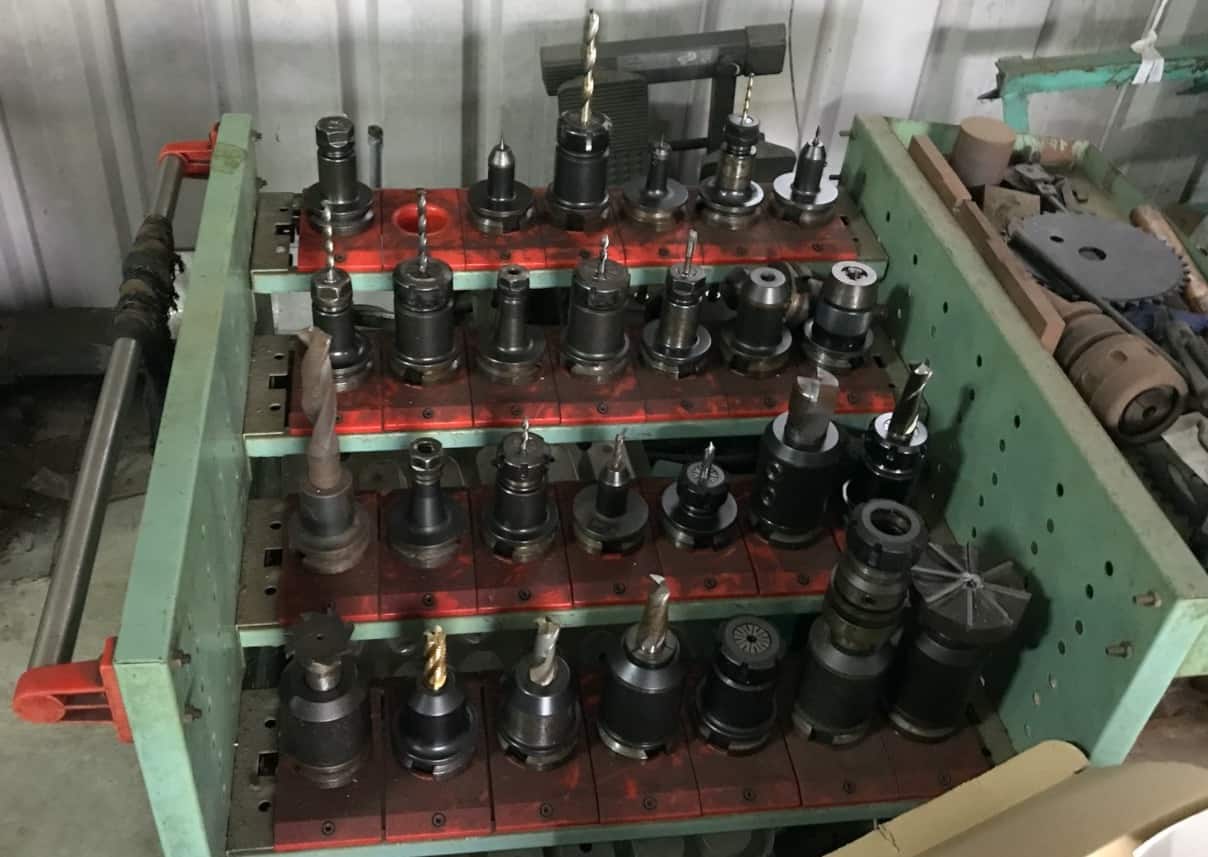
An example of a range of cutting drill bits and milling pieces: there’s a bit for every job.
High-end CNC machines automatically swap out cutters should a batch require different forms of processing across multiple sequences.
The operator keeps an eye on the processing, his only interaction with the machine being clean up tasks like blowing off detritus, swapping out components and punching a few keys here and there to fine tune a process.
Forms of Processing
Processing can be either basic or complex.
I’ll firstly cover complex processing in which we at SCADA are in a league of our own.
Complex Processing
We use over a dozen high-end CNC machines to execute precision cutting routines on a variety of specialized components.
Video begins at the CNC milling section.
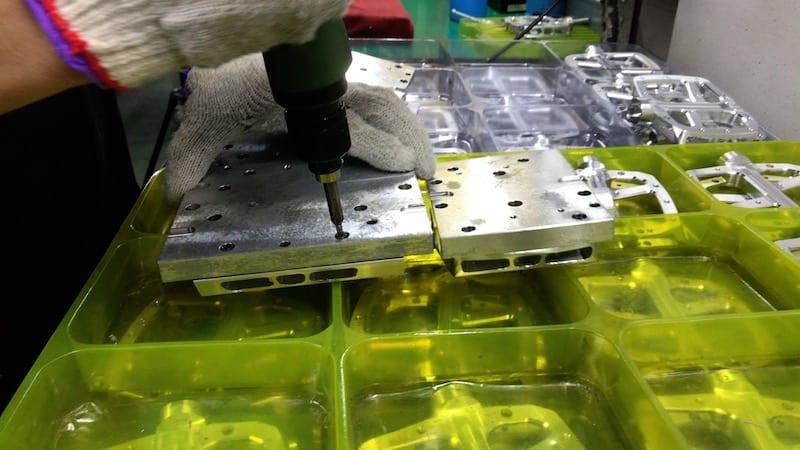
To process pedals we bolt them to a plate in pairs.
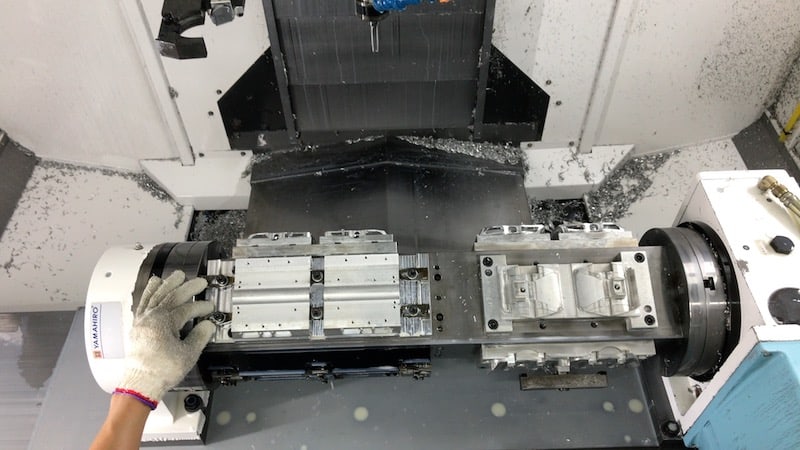
Four sets of plates are fixed into position next to another set of four.
The cutter moves across the plates on top; the carrier revolves; the cutter repeats the cutting action until all 16 pedal platform blanks have been processed.
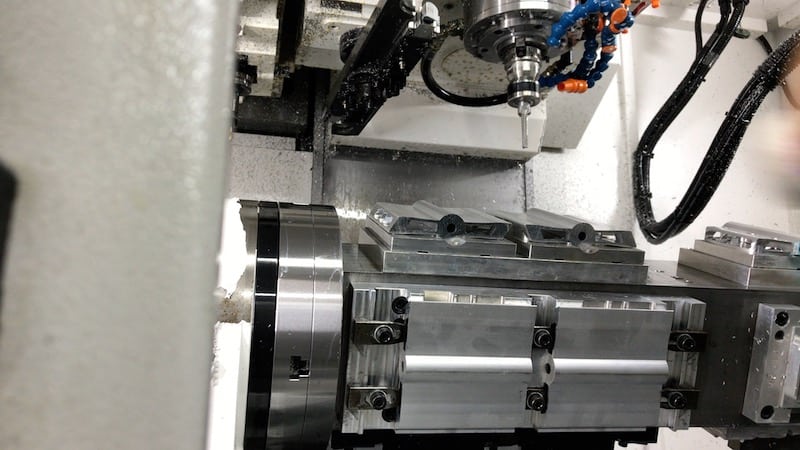
The cutter can only cut one pedal at a time.
Time is saved since a batch of 16 can be processed in one go, without having to swap out components.
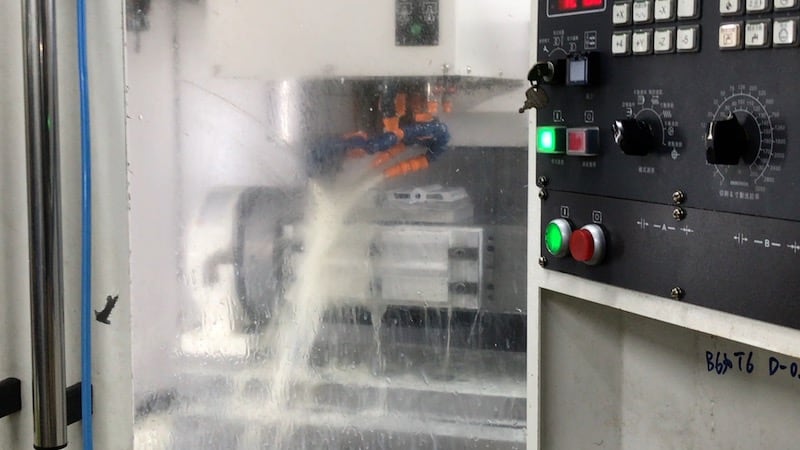
The cabinet is closed, the sequence starts, with jets of fluid dousing the contact point of the cutter on the pedal blank.
Basic Processing
As an example of basic processing, this machine is for drilling multiple grip-pin holes in mtb flat pedals, and was built specifically to perform this task.
Video begins at the basic drilling section.
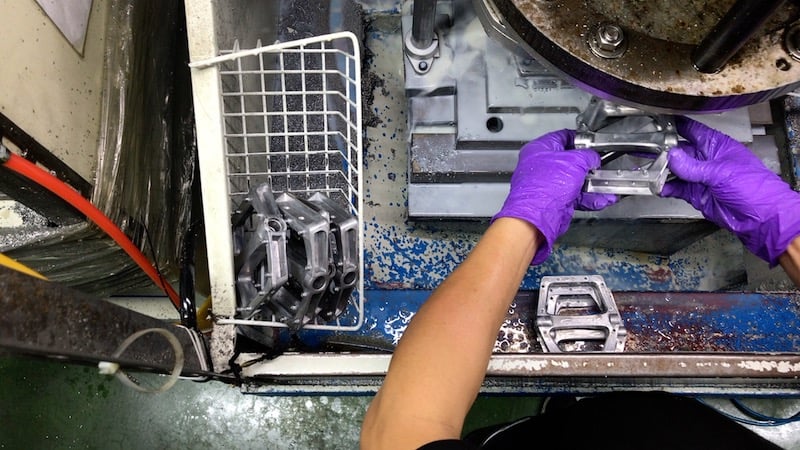
It’s a very basic ‘CNC’ machine since the sequence is a simple up and down motion with the drill bit depth the key variable.
The batch here is being processed two at a time.
Mount two pedals on the machine for rapid processing. Then remove and replace.
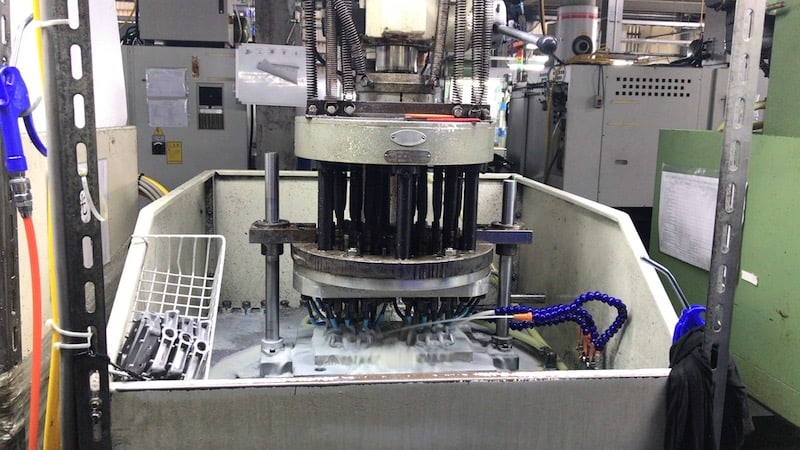
The fluid lubricates and cools the bits. It also prevents detritus from any possibility of being ejected from the cut, captures the offcuts, then carries them away.
Normally CNC processing is enclosed in cabinets, as we saw above. Since the use of fluid and the cutting head (drill bit) remaining in one spot removes any danger of flying particles, an open basin is fine.
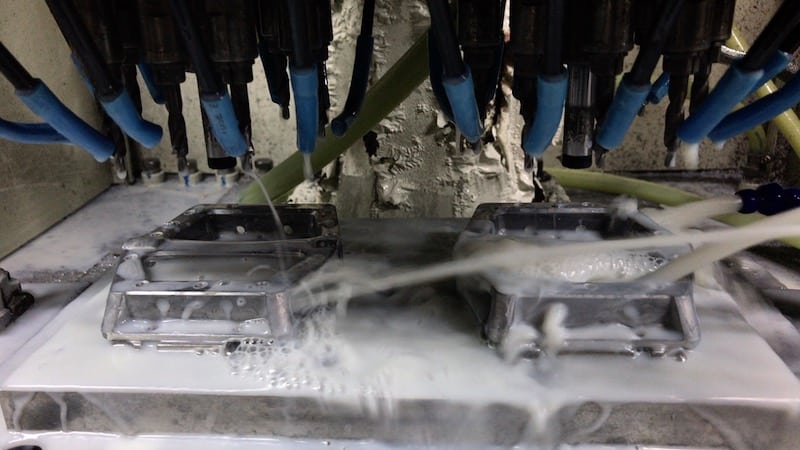
The drill bits descend, cut, then retract; the fluid sprays the pedals and drill bits only when the cutters are in motion.
The fluid is filtered, cleaned and recirculated—there is no effluent released into surrounding waterways.
One of the reasons a higher-end CNC machine is so expensive is the complicated fluid circulation which simultaneously cleans away cutting detritus and cools the cutters’ contact areas.
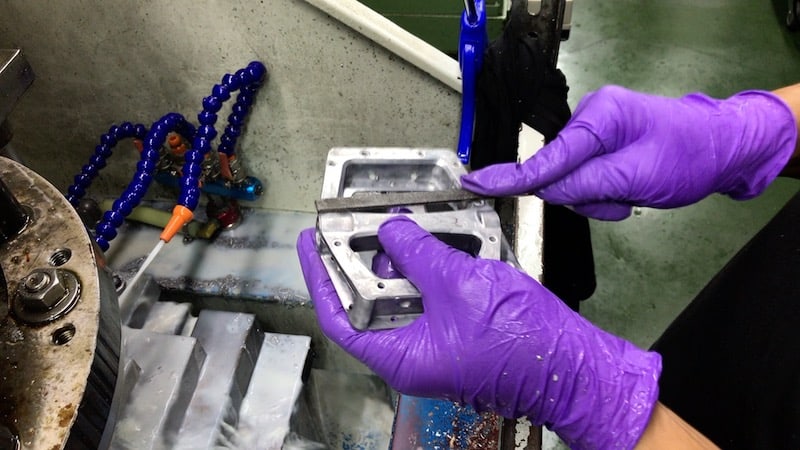
Drilling holes occasionally leaves a slight edge requiring a rub with a file.
ASSEMBLY STAGE
Most assembly at SCADA is carried out on many short production lines with usually one — sometimes two — personnel carrying out the assembly procedures.
Materials — components and pedal bodies — enter at one end.
The components are assembled into the pedal bodies.
Then the finished pedals are packaged and boxed up ready to ship.
One, or sometimes two, lines are devoted to a brand’s production of one model.
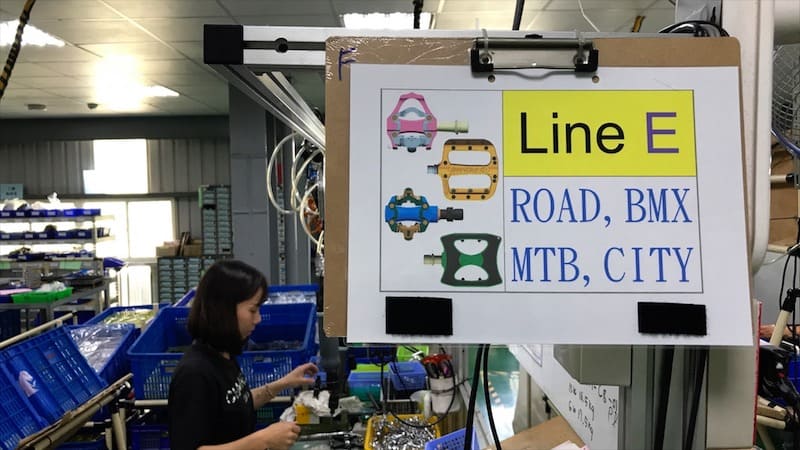
Or, as in this case, a mixture of models is assembled where each is to be fitted with the same bearings and/or axles.
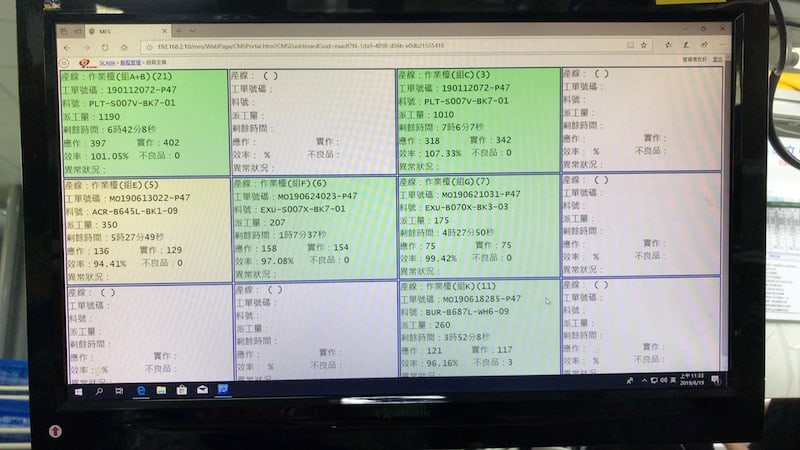
The MES platform is the means by which we manage and maximize production jobs across the assembly area.
Video covers the MES section.
One screen is mounted at the end of each line; another is monitored by the floor manager who can respond to bottlenecks quickly.
Each square records the details of each line’s production.
Each green square indicates the rate of assembly meets the requirement: there are no bottlenecks, which are normally caused by tool malfunction or where resupply of components is lagging.
Problems are indicated by a square turning yellow; the change is generated by a drop below 85% in production efficiency.
When the problem is solved and the production rate is raised above 85%, the square turns green—production is back on track.
Pedal Body Assembly
The assembly routine involves installing the axle together with an injection of grease. Then the bearings are pressed into position.
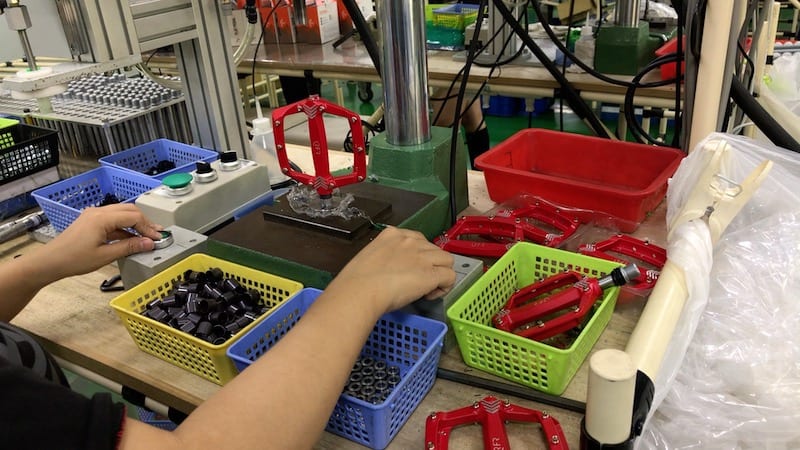
You’ll see a brace of axles on the top left of the image with the grease injection machine located in the very top left.
Bearings are pressed in and the internal axle bolt is tightened to tolerance with a small torque wrench and closed up with the end nut.
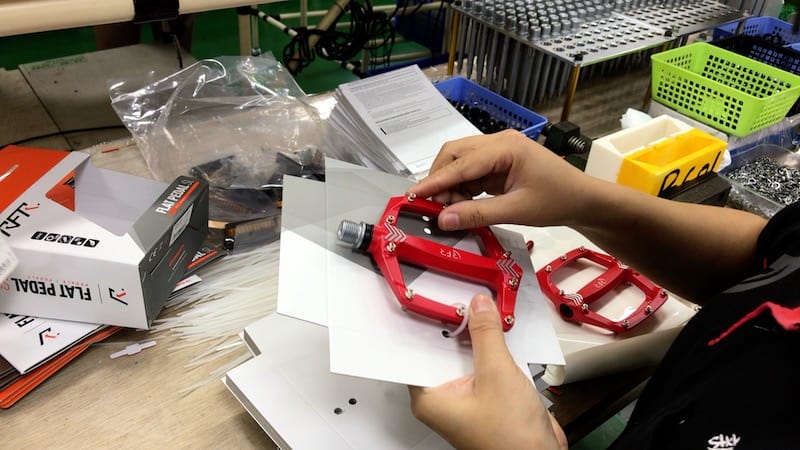
Finished pedals are bound to the interior packaging of the product boxes in which they’ll be shipped.
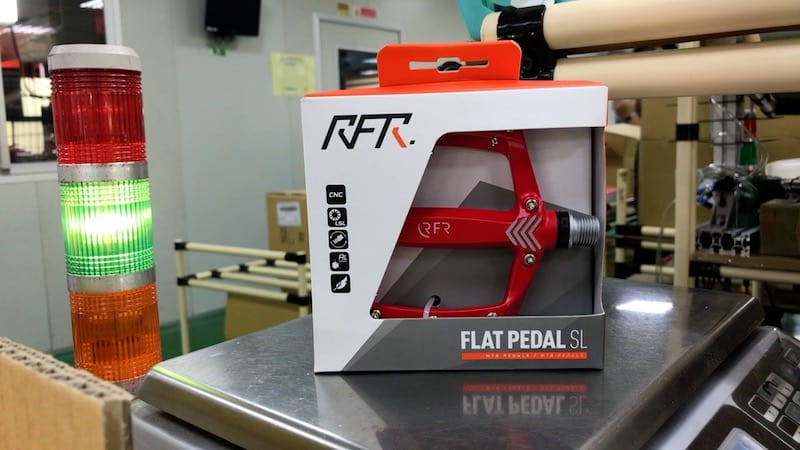
Advanced Customized Automation
The continual improvement of production is one of SCADA’s key operating principles.
There are two interrelated advantages:
- Cuts costs
- Delivers higher quality productions to our customers
Building customized manufacturing solutions is a key means for achieving this.
Video begins at the screw dispenser section.
For example, we designed and built a machine for automating the installation of cleat brackets to mtb or hybrid pedals.
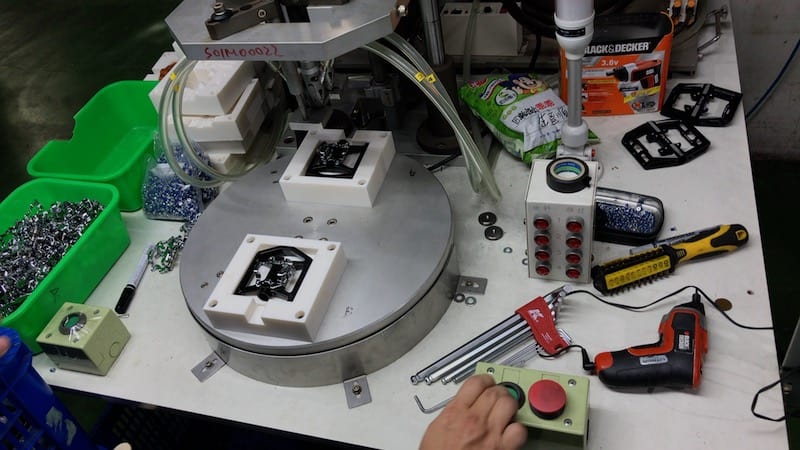
One operator can attach hundreds of brackets to their pedal bodies using this machine.
Load a pedal body on the platform, position the bracket on the pedal body, hit the button to engage the screw applicator—4 screws fastened into place and securing the bracket to the pedal body in one movement.
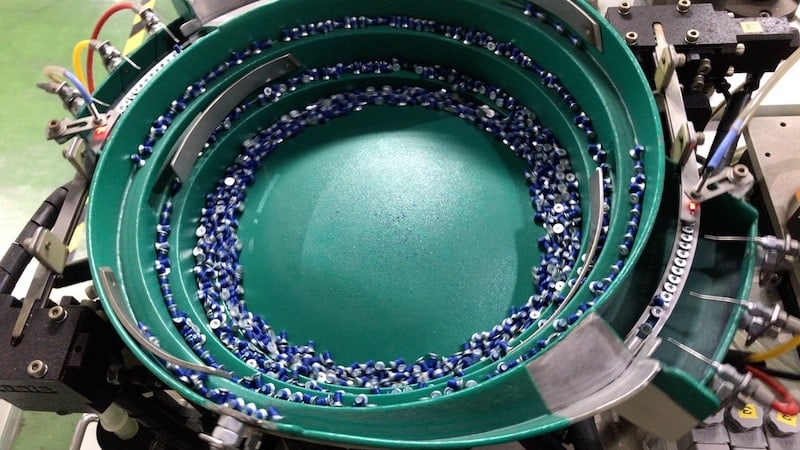
We load the screws into a tray at the back of the machine which feeds them through to the applicator directly above the operator’s platform ready for installation into the pedal body.
TESTING STAGE
The two main components that are the focus of testing are
- Sealed bearing durability and longevity
- Axle strength and durability.
1. Sealed Bearing Longevity
A quality pedal is one containing a bearing that does not grind itself to pieces before its time.
Testing a sample from a new production, the ISO requirement is to test to 100,000 cycles.
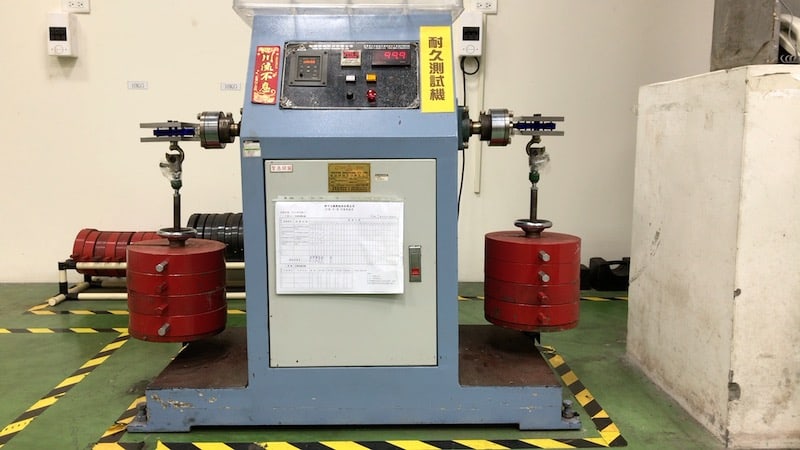
At SCADA we actually test to 1,000,000 cycles at the prescribed load.
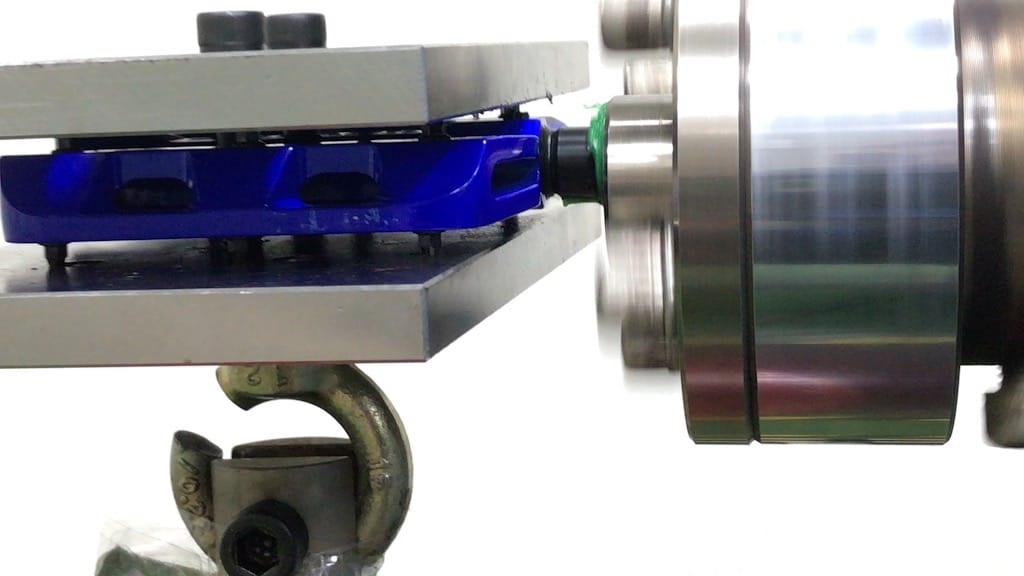
The axle and bearing must carry the load without failure through the whole test.
2. Axle strength and durability
The pedals on an MTB hurtling along a rough and rocky trail are the most vulnerable components apart from the derailleur cage and the chain ring.
Sticking out at 90 degrees to the crank, sooner or later a pedal will impact a rock on rougher downhill sections.
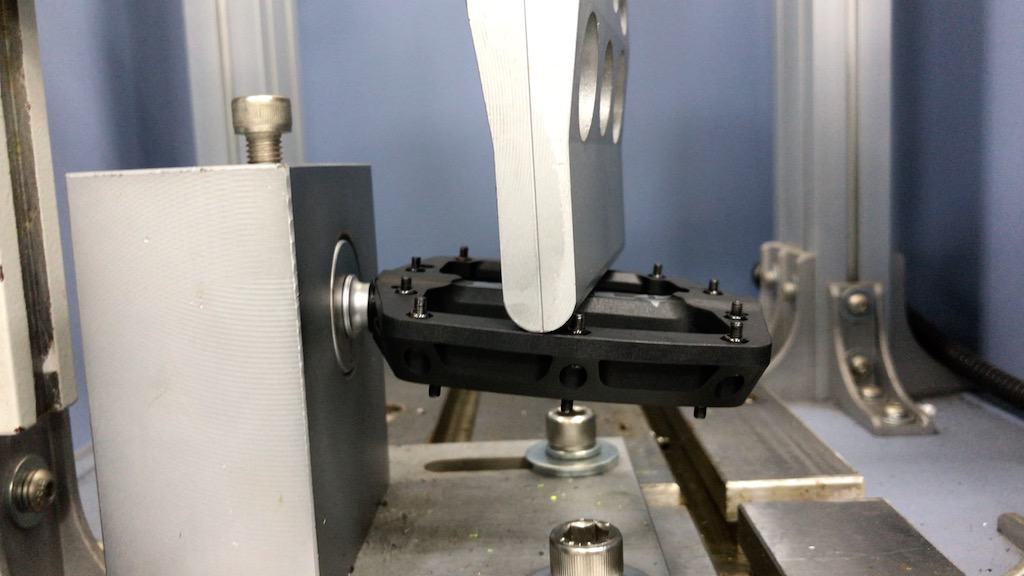
A quality pedal axle won’t snap but will most likely bend between the threads and where it enters the pedal body.
We send the blunt end of the hammer into the center of the pedal body which will eventually bend under a force many times greater than forces generated from an impact on the trail.
If it bends as predicted and does not snap, it is deemed to have passed the test.
FINAL COMMENTS
There has been an increase in the range and complexity of pedals over the last two decades.
Many specialist bike brands have appeared, each serving its own highly motivated community.
SCADA aims to service big brands and small alike and have adapted our procedures to be able to accept small orders with small, growing brands especially in mind, making us unique amongst the relatively small pool of pedal manufacturers in business today.
If you are a brand in the market for a quality pedal, get in touch.